Almost 20 years with a firm eye on C-parts
Almost 20 years with a firm eye on C-parts
History of Würth Industrie France
1945 – From the beginning
History is written by people. People like Prof. Dr. h. c. mult. Reinhold Würth, who in 1945 founded the company that bore his name: Adolf Würth GmbH & Co. KG. This laid the foundation for the Würth Group. Formerly the Industry Division in the parent company Adolf Würth GmbH & Co. KG in Künzelsau, Reinhold Würth recognised the potential of supplying industrial customers and the associated growth market. And so, Würth Industrie Service was founded on 13 January 1999 as an independent subsidiary at the Industriepark Würth business park in Bad Mergentheim. The Industriepark Würth business park at the Bad Mergentheim site in central Germany was the ideal location for the company's activities. The former Deutschorden-Kaserne barracks has served as the corporate headquarters of Würth Industrie Service for over 20 years. The Deutschorden-Kaserne barracks on the "Drillberg" in Bad Mergentheim was closed when the armed forces across Europe were reduced in size in the early 1990s. The armoured brigade 36 that was stationed there was relocated and taken out of service in 2003. The barracks site was acquired by the Würth Group in 1999 and converted by Würth Industrie Service into a European logistics centre using the existing infrastructure to serve industrial customers.
2000 – A step into independence
On 1 January of the new millennium, Würth Industrie Service took over the business of the industrial division of Adolf Würth GmbH & Co. KG. At first, the idea of employing 88 people over an area of 122 hectares seemed inconceivable. But the figures and success story over the years have proven the founders of the company right. This step was made possible by the joint efforts of all colleagues. Another milestone this year was the inauguration of the Kanban logistics centre in February. It has a total area of 11,000 square metres. With a total of 9200 pallet spaces and over 100,000 shelves, there really is room for a whole lot of goods! On 22 and 23 July 2000, Würth Industrie Service presented itself to the general public for the first time with an open day event. The number of visitors was huge, with over 100,000 guests!
2003 – Creation of Würth Industrie France
Würth Industrie France S.A.S. was created in 2003. Formerly the Industry Division of Würth France S.A., Würth Industrie France began its cooperation with its sister company Würth Industrie Service in Bad Mergentheim, Germany, which became the logistics center for Europe. The first turnover of the new independent company Würth Industrie France was 10.6 million euros.
In addition, work to expand the Kanban warehouse by an additional 5500 pallet spaces over a floor area of 2000 square metres began. The numbers were eye-opening – 15,000 pallet spaces, 45 metres high.
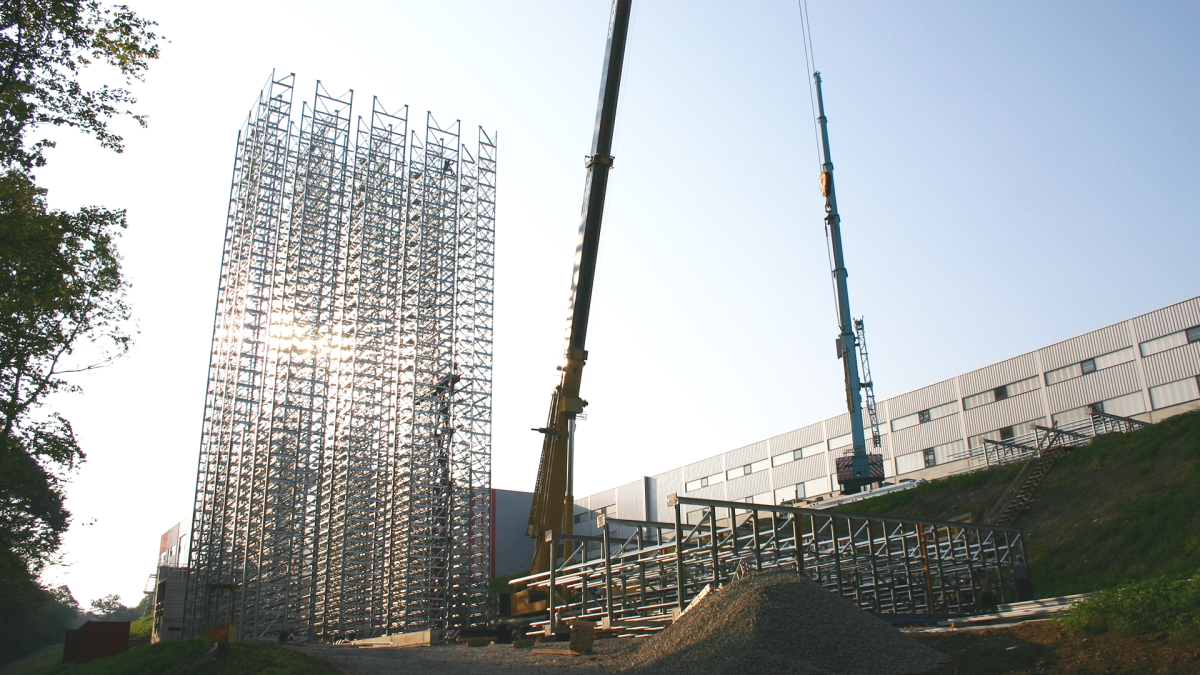
Ongoing construction of the new high-bay warehouse (N07)
2004 – Ongoing improvements
In 2004, a plan was drawn up for a corresponding warehouse on the Drillberg. This was followed by the initial groundbreaking for the first construction phase of the new high-bay warehouse (N07). At this time, the incoming and outgoing goods warehouse on the Drillberg was annexed as a new building to the high-bay warehouse in Building N06. From the beginning of 2005, the new EU countries were also supplied from Bad Mergentheim, and the WINWORK® (Würth Industrial Network) began to grow. WINWORK® companies in India and China consolidated the industrial network in Asia.
2005 – First certification for Würth Industrie France
Würth Industrie France successfully obtains ISO 9001:2000 certification.
2006 – WINWORK® continuously growing
The worldwide industrial network WINWORK® continued to grow. Companies in Brazil and South Africa, as well as a new branch office in Great Britain, strengthened the industrial network.
Würth Industrie France achieved a turnover of 16.6 million euros, i.e. an increase of 27% compared to 2005 (13 million euros). The objective of 20 new Kanban system customers was reached. The number of employees at Würth Industrie France has risen to over 60.
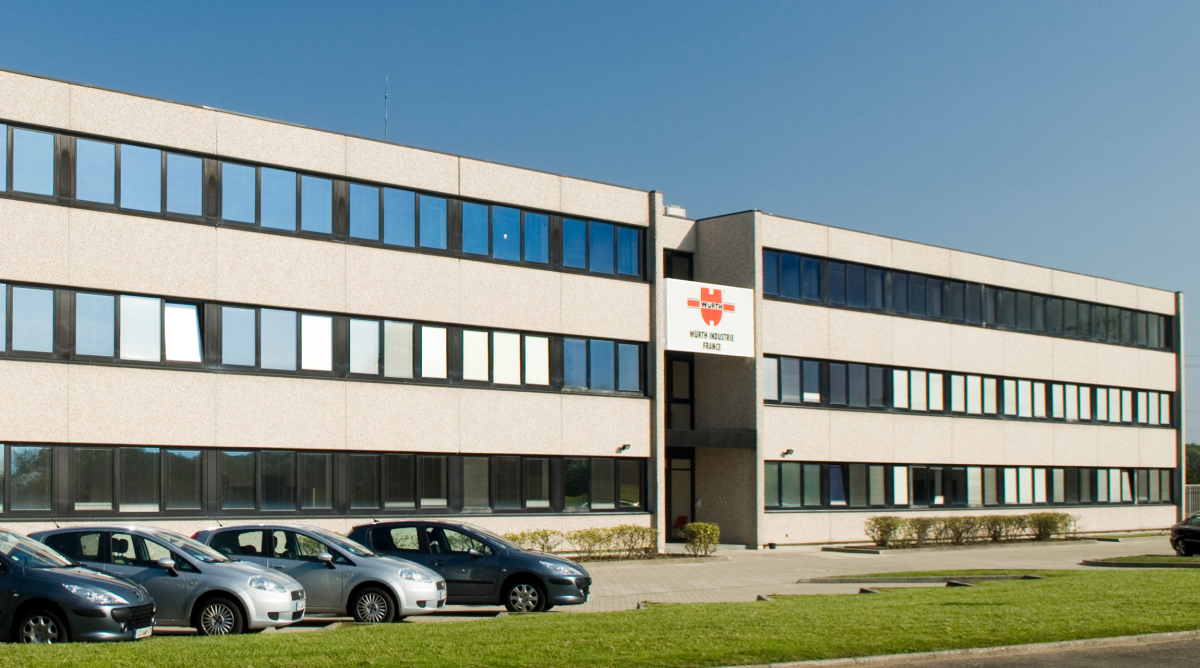
Head office of Würth Industrie France, 2007
2007 – Head office that thinks bigger
A project to move to new premises in Erstein-Krafft has been validated by the Group's Management in order to cope with the company's growth. The company is therefore moving in August to its new headquarters with a surface area of 2,500 m², allowing for serene growth in the years to come. At the end of 2007, the company has 72 employees, 42 of whom work at our site in Erstein-Krafft. Würth Industrie France achieved a turnover of 23.4 million euros, which represents a growth of more than 40% compared to 2006. We were also able to achieve our target of 25 new Kanban customers.
In our logistics center in Bad Mergentheim, a second high rack warehouse (N08) is built and directly connected to the existing high rack warehouse (N07).
2008 – Third consecutive year of achievement
With a turnover of 28.7 million euros and an increase of 22% compared to the previous year, 2008 is the third consecutive year of achievement of the planned objectives. The workforce contains 82 people. In 2008, our European Logistics Center recorded more than 700,000 active Kanban bins at our customers.
2009 – Major innovation in Kanban logistics
The year 2009 began with a major innovation in Kanban logistics: the development and introduction of the patented W-KLT® (Würth small load carrier). This was followed by a string of awards, such as the 2009 Deutscher Logistik-Preis (German Logistics Prize) for the project "Modular Logistics: The Solution for Multi-Channel Distribution" or the Bambus-Champion 2010 award. The annual award honours companies that stand out from the competition due to above-average growth, innovation or other success factors. In 2011, the WIN-WIN CUP was awarded for the best customer-supplier relationship of the decade between the Liebherr Group and Würth Industrie Service.
2009 is also the year that Würth Industrie France felt the impact of the global economic crisis, but was able to resist by achieving a turnover of 22.5 million euros. The constant evolution of our customer base, and especially a new record of 30 new Kanban customers, show the relevance and attractiveness of our service offer. The number of employees at the end of 2009 was 76.
2010 to 2011 – Continuous growth
With a turnover of 28.2 million euros, comparable to the 2008 result, Würth Industrie France was able to quickly return to growth. This result represents an increase of 25.3% compared to the previous year. The company has 23 additional Kanban customers and 85 employees.
2011 was a record year for turnover, which reached 37 million euros, an increase of 31.2% compared to 2010. Würth Industrie France has 25 new Kanban customers. In September 2011, the European Logistics Center expanded with the construction of three new buildings entirely dedicated to Kanban.
2012 – Year of innovation
The year 2012 brought some significant innovations. The brand exceeded 1,000,000 items in the industrial range, the new Kanban container W-KLT®2.0 was officially ready for production as a further development of the revolution in Kanban logistics, the ORSY®mat 3.0 was introduced as an innovative output system for managing C-part requirements in material management
Würth Industrie France has now more than 100 employees and this year's turnover reached 40 million euros. The number of Kanban customers reached 170 at the end of 2012.
2013 – Continuous innovation and new building developments
The iBin® camera module was released in 2013 as an optical ordering system that revolutionised the entire material management process over the long term. The goal of the iBin® is to link and automate C-Parts management and direct workstation supply in real time. The new iBin®WP heralded the industrial revolution in C-parts management: Industry 4.0 – The person at the centre of a networked system world. Networked systems – Digital. Real. Transparent.
On April 1, 2013, Würth Industrie France celebrates its 10th anniversary as an independent company within the Würth Group. After the acquisition of the building in 2012, Würth Industrie France began major work to adapt its headquarters to the growing number of employees, which now numbers 105. The head office has two new parking lots, a new entrance and a new showroom. The turnover has increased by more than 5% to 42.2 million euros. The number of Kanban customers increased to 180.
2014 – Expansion of our logistics solutions
In 2014, Würth Industrie France achieved a turnover of 43.2 million euros, an increase of 2.5% compared to the previous year. At the end of December, the number of employees was 108. Two innovations have been added to our logistics solutions to support our industrial customers:
These are two flexible hanging systems for the individualized organization of your workstations with a view to optimizing production processes.
At the same time, we are developing our Kanban logistics services with the installation of our first systems equipped with the RFID innovation to go even further in real-time supply.
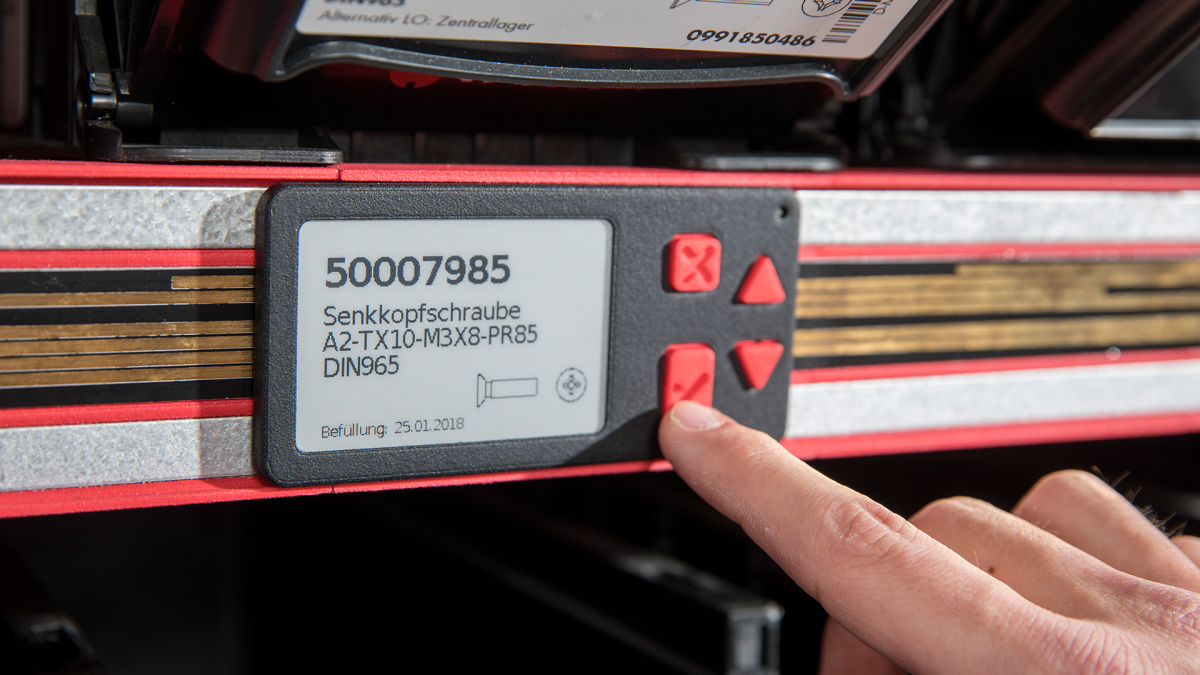
iDisplay & CPS®Mobile: Networked systems
2015 – Networked systems development
The year 2015 is marked by the installation of the first ORSY®mat vending machines in France, designed to manage consumables and MRO products. Würth Industrie France continues to grow, recording a turnover of €44 million and a workforce of 109.
In cooperation with the Fraunhofer Institute for Material Flow and Logistics (IML), the iDISPLAY was developed in 2015. The CPS®MOBILE app opens up an additional management system and offers a transparent exchange of information and data.
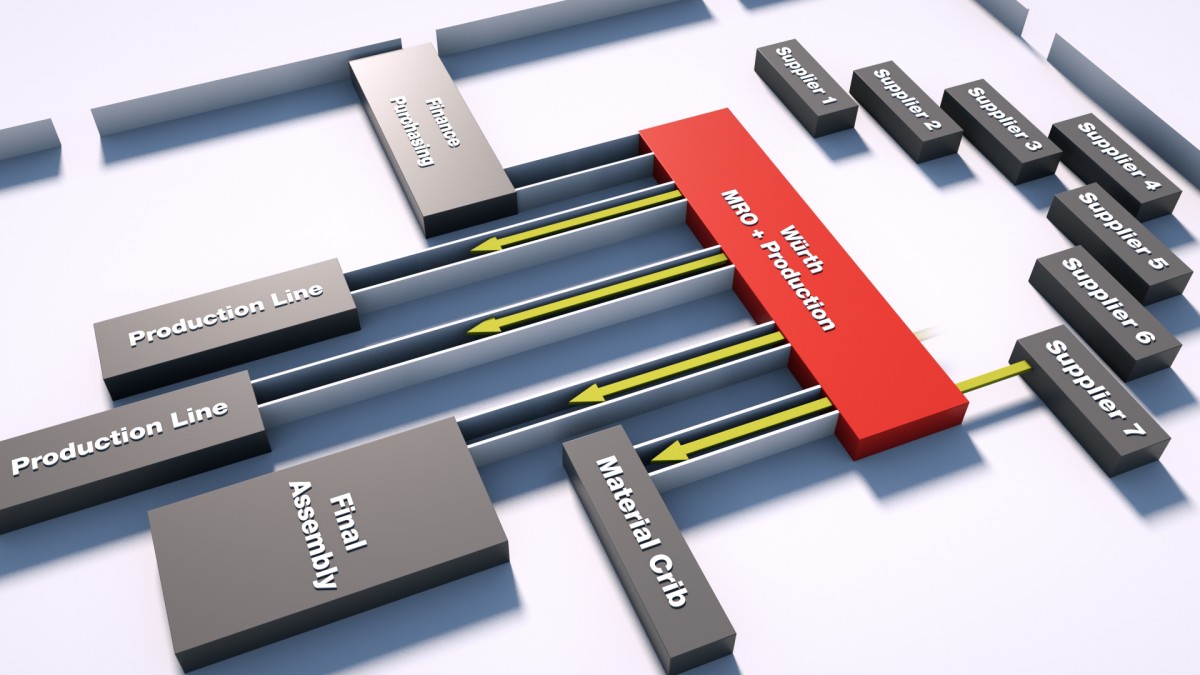
Is your factory really lean? From a supplier to a networked partner
2016 to 2017 – From a supplier to a networked partner
In 2016, Würth Industrie France achieved a turnover of 44.8 million euros and continues to grow, now employing 113 people. In 2017, Würth Industrie France increased its turnover by more than 7% to 48 million euros and a workforce of 130.
Is your factory really lean? Gone are the days when supplying companies with C-parts involved nothing more than delivering the required item. These days, the supplier has developed into a partner that is integrated into the process landscape of a company, and supports the company in being networked in the digital and physical world through comprehensive systems, services and information media. Since 2017, the expansion of the high-bay warehouse has increased storage capacity by more than 49,000 pallet bays to around 650,000 storage slots, of which 150,000 alone are for pallets. The test lab for Würth Industrie Service was accredited as an official testing centre. The iPLACER® was added to the RFID range.
2018 – Thinking global
In 2018, with CPS®miLOGISTICS items from outside Würth are integrated into C-parts management along with standard and special parts, and they are included in the automated Kanban supply for Würth Industrie France.
In 2018, the number of employees at Würth Industrie France reached 138. The company reached a new milestone by reaching the symbolic mark of 600 RFID Kanban customers in Europe. A new unit was created within our company: Innovative Systems, dedicated to the ORSY®mat logistical study (automated inventory management solution), assistance and technical support to our customers. The ORSY®mat vending systems allow the management of Würth product ranges such as MRO products, PPE, small tools and space-saving machines.
2019 – Tourné vers l'avenir
In 2019, the innovation factory grew when innovative automated technologies such as the ORSY®mat WGT and ORSY®mat CHE were added to the Würth Industrie France range as further solutions that allow users to digitalise their entire supply chain and make this supply chain more transparent.
Further investments to expand our european logistics center are being implemented, including the expansion of the high-bay warehouse by 30,000 bays. The expansion of the Würth Industrie Service logistics centre is an ongoing endeavour. Between 2018 and 2020, a total of EUR 160 million has been invested in expansion measures to ensure security of supply for customers. The company plans to start operations in this regard in 2020.
1999-2019: Würth Industrie Service, the sister company of Würth Industrie France, celebrates its 20th anniversary.
Würth Industrie France has 136 employees. Important works are started in 2019: an extension of our building with the construction of a 2nd parking lot and a project of fitting out the 2nd floor is born.
2020 – Stable C-parts management
The Covid-19 pandemic in 2020 has proven once again how important it is to have a stable C-Parts management and the role of digital and contactless technologies. With the study of an RFID pallet box, an open system for automatically triggering orders by continuously scanning the surroundings for RFID tags, Würth Industrie France is expanding its portfolio by adding more solutions, which can help the users to digitalise and transparently design their entire delivery chain. The study on ORSY®mat CBL, a vending machine for supplying cables, wires, cords and installation material to the customers, assures maximum certainty in materials management. To ensure utmost safety in the workplace, the company has introduced professional hygiene solutions to its workplace systems of the CPS®IWS product line in the wake of the pandemic. The fact that Würth Industrie France is driving digital transformation is proved not only by the technologies in automated C-Parts management but also by the opportunity to interactively experience the range of services offered by the company. The virtual showroom WIS Virtual Experiences presents system solutions as well as product range for an efficient C-Parts management as well as offers a suitable setting for customer visits.
2020 is, despite the unprecedented situation, a year of novelties and adaptation:
- Installation of the 1st ORSY®Push in France, the latest innovation in ORSY® shelving.
- Installation of the 1st ORSY®mat WGT in France. This new vending machine is equipped with scales that detect the number of articles withdrawn and trigger their replenishment as soon as the doors are closed.
Expansion work has begun at Würth Industrie France, the construction of the 2nd floor started.
Our ORSY®mat vending machines are suitable for Covid-19 control products.
The parent company of the Würth Group, Adolf Würth GmbH & Co. KG, is celebrating its 75th anniversary.
2021 – A strong identity
The economic upturn that began at the end of 2020 continued into 2021. Würth Industrie France also participated in this trend, with sales increasing by almost 30%.
This development of the Industry division has led us to develop our own identity through the creation of a dedicated logo, validated by the Würth Group. From now on, the English term "INDUSTRY" will complement our existing Würth logo.
Worldwide, the WINWORK® recorded sales of 1.911 billion euros in fiscal year 2021.
The Kanban system based on the "just-in-time" principle continues to expand. The testimonies of customers with a Kanban installation prove once again the attraction of industrial companies for this system. In 2021, more than 175,000 bins are in circulation at various customers.
Würth Industrie France is also expanding its portfolio by adding other solutions, which can help users to digitize and design their entire supply chain seamlessly.
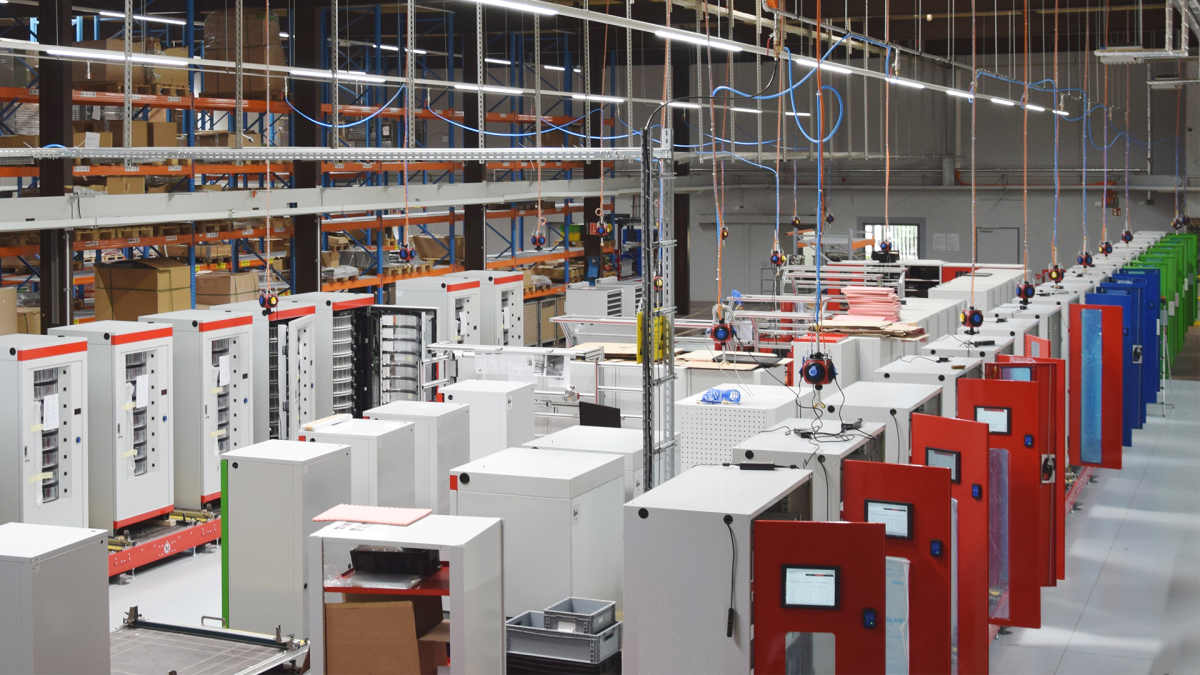
New ORSY®mat storage and configuration facility in Boxberg, Germany
The RFID system family and the iSHELF® smart shelf are celebrating their 10th anniversary. After conducting the first tests with RFID technology in 2008, we launched the first serial products under the CPS®RFID brand about 10 years ago. Some figures: 57 RFID clients, 61 transponders and 252 iSHELF® were installed in 10 years.
The first iPLACER® was installed in France in 2021; it is a practical battery-operated module for scanning bins and/or pallet cards in an instantaneous way. As soon as there is a need, the card must be placed in front of the box and the order is generated (via RFID tag).
Würth Industrie continues to invest in its core business, systems, and opens a new ORSY®mat storage and configuration facility in Boxberg, Germany. Closer cooperation and expertise in one location will enable further development of our facilities. Since 2015, more than 70 ORSY®mat have been installed at our customers.
2022 - Historic Record
The Würth Group has broken its own sales record by reaching 19.95 billion euros in 2022. Worldwide, the Group now employs 85,637 people.
Würth Industrie France also contributed to this success by closing the year with 89.2 million euros. This record was made possible by the daily work of our 157 employees.
Following the expansion of the headquarters, which began in 2020, the existing premises are now being renovated. This more modern and more eco-responsible working environment will allow us to serenely welcome the company's future developments. As part of our CSR (Corporate Social Responsibility) approach, Würth Industrie France is continuing its actions to make its employees more eco-responsible, in particular through the implementation of waste recycling and the use of recycled paper.
2023 – 20 years later
The year 2023 marks the 20th anniversary of the company's creation. Würth Industrie France and its 153 employees were able to mark the occasion by closing the year with a record turnover of 96.2 million euros. The Würth Group is also pushing its limits by reaching a turnover of 20.4 billion euros in 2023 with the support of its 87,047 employees.
2023 also marks the tenth anniversary of the ORSY®mat. Since the beginning, our range of vending machines for managing consumables has expanded to now offer 6 variants: ORSY®mat FP, ORSY®mat HX, ORSY®mat RT, ORSY®mat DR, ORSY®mat WGT and ORSY®mat CHE.
The company is also continuing its efforts to produce carbon-free electricity by installing 256 solar panels. This clean electricity intended for the building's consumption also supplies the 16 charging stations used to recharge our fleet of electric vehicles. The objective at this stage is to achieve coverage of 30% of total consumption.
The Würth Industrie Service GmbH & Co. KG collects and processes the personal data provided in the form in order to process the requested request for you. Please note the mandatory fields in the forms. The legal basis for this processing, the absolutely necessary data, is Art. 6 para. 1 lit. b DSGVO, implementation of a pre-contractual measure. The processing of data voluntarily provided by you is carried out on the basis of Art. 6 para. 1 lit. f DSGVO. Thereafter, processing is permissible which is necessary to safeguard our legitimate interests. Our legitimate interest is to have contact with you, our customers, to improve our consulting quality and to be able to contact you more easily in case of possible queries. The data collected will only be stored by us for as long as is necessary to process your enquiry and to contact you. They are then deleted.
Supplementary data protection information, in particular regarding your rights to information, correction, deletion, restriction of processing, objection and complaint, can be found in our data protection declaration.