Procedural overview - 3D printing
A characteristic feature of all 3D printing procedures is the layer-by-layer application that creates the final component.
As a global solution partner, Würth Industrie Service assists you in all 3D printing procedures.
The procedure in detail
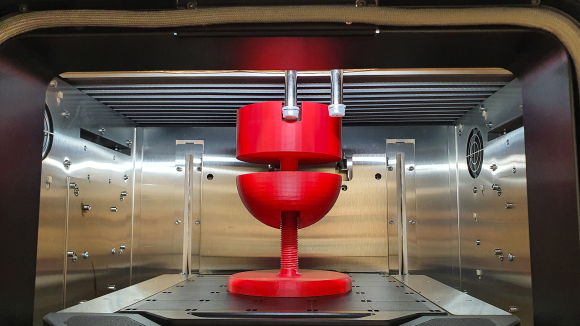
Fused filament fabrication
Thermoplastic filament is melted in the print head, and applied in layers with a carrier material in a cordlike form.
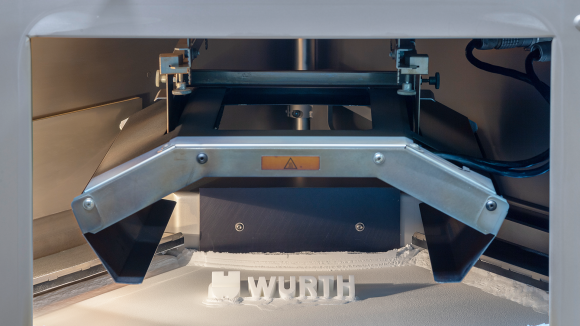
Laser sintering
Plastic powder is added in layers using a recoater in a pre-tempered space, and then the contours are fused together with a laser beam.
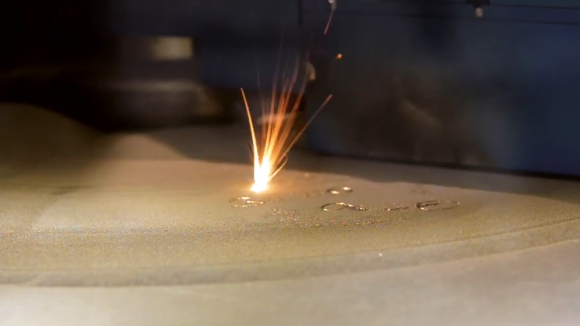
Metal 3D printing
Powdered metal is added in layers using a recoater, and then the contours are completely and locally re-melted with a laser beam.
Materials and Technical data
- Aluminium (ALSi10Mg)
- Titanium (TIAL6V4)
- Stainless steels (1.4404, 1.4542, 1.4057)
- Tool steels (1.2709)
- Inconel IN 718
- Hasteloy X
- Coating thickness 15 – 500 µm
- Average roughness Rz 20 – 50 µm
- Accuracy in 3D printing ± 0.2 mm
- Polyamide 12
- Aluminium-filled polyamide
- Marble-filled polyamide
- Flame-retardant polyamide
- Polyamide TPU 92A-1
- PEI
- Polypropylene (PP)
- ABS, PLA, ASA
- Temperature resistance 40 – 220 °C
- Accuracy in 3D printing ± 0.2 mm
- Achievable coating resolutions 0.016 – 1.5 mm
Finer surfaces and higher accuracies can be achieved by subsequent post-processing. The maximum dimensions of the components depend on the manufacturing processes and the manufacturing material. Additional materials are available on request.
Additional information
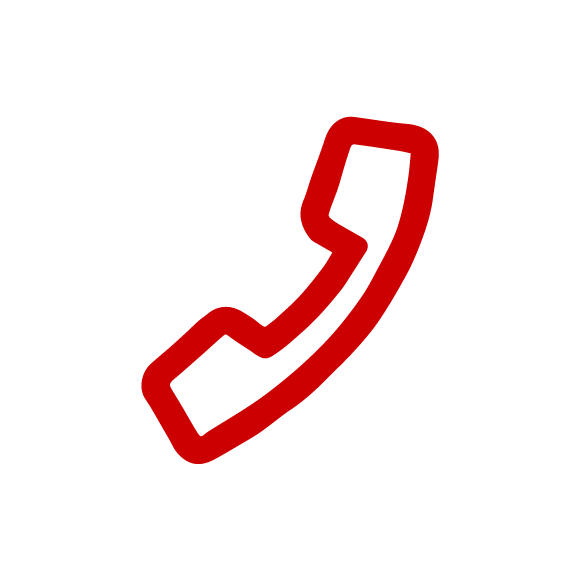
Contact
We are here for you!
Please contact us by telephone +49 7931 91-3288 or
via E-Mail under additivemanufacturing@wuerth-industrie.com.
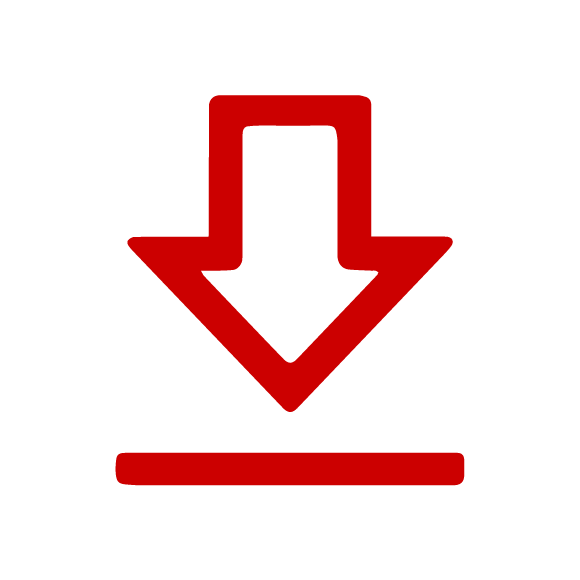
Websites can save or retrieve information in your browser in the form of Cookies. This may be anonymous statistical data, information about you, your settings or devices used, in order to enable a personalised web experience or so that the website works in the way you are expecting it to.
We respect your right to protection of your data. You can therefore decide not to accept certain types of Cookies. For an overview and the settings for the Cookies which we use, please see here. You can change these settings at any time, by invoking our Data protection declaration.
By saving, you confirm that you have understood the settings specified for Cookies and that you agree with them.
The Würth Industrie Service GmbH & Co. KG collects and processes the personal data provided in the form in order to process the requested request for you. Please note the mandatory fields in the forms. The legal basis for this processing, the absolutely necessary data, is Art. 6 para. 1 lit. b DSGVO, implementation of a pre-contractual measure. The processing of data voluntarily provided by you is carried out on the basis of Art. 6 para. 1 lit. f DSGVO. Thereafter, processing is permissible which is necessary to safeguard our legitimate interests. Our legitimate interest is to have contact with you, our customers, to improve our consulting quality and to be able to contact you more easily in case of possible queries. The data collected will only be stored by us for as long as is necessary to process your enquiry and to contact you. They are then deleted.
Supplementary data protection information, in particular regarding your rights to information, correction, deletion, restriction of processing, objection and complaint, can be found in our data protection declaration.