Customer reference: Lindauer DORNIER GmbH – Maximum availability of materials through ORSY®mat
Peter Dornier, son of the famous aviation pioneer Claude Dornier, founded Lindauer DORNIER GmbH in 1950. With its product lines of weaving machines, special machines (systems for film production) and composite systems, DORNIER is a technology pioneer. For more than 50 years, the company’s weaving machines, which are used to manufacture products that include high quality fabrics like airbags and filter fabric, have set the standard for the processing of high-performance fibre like carbon, glass and aramid. DORNIER is the market leader in engineering and production of film stretching lines for manufacturing ultra-thin plastic films. Along with the packaging industry these films are also used in solar cells, lithium-ion batteries, semiconductors, capacitors and in displays of smartphones, flat screens and tablets. In composite systems, DORNIER combines its decades-long experience in design and manufacturing of weaving machines and film stretching lines for manufacturing of customised systems for the production of high-quality fibre composite components for aircrafts, vehicle bodywork and lifestyle products.
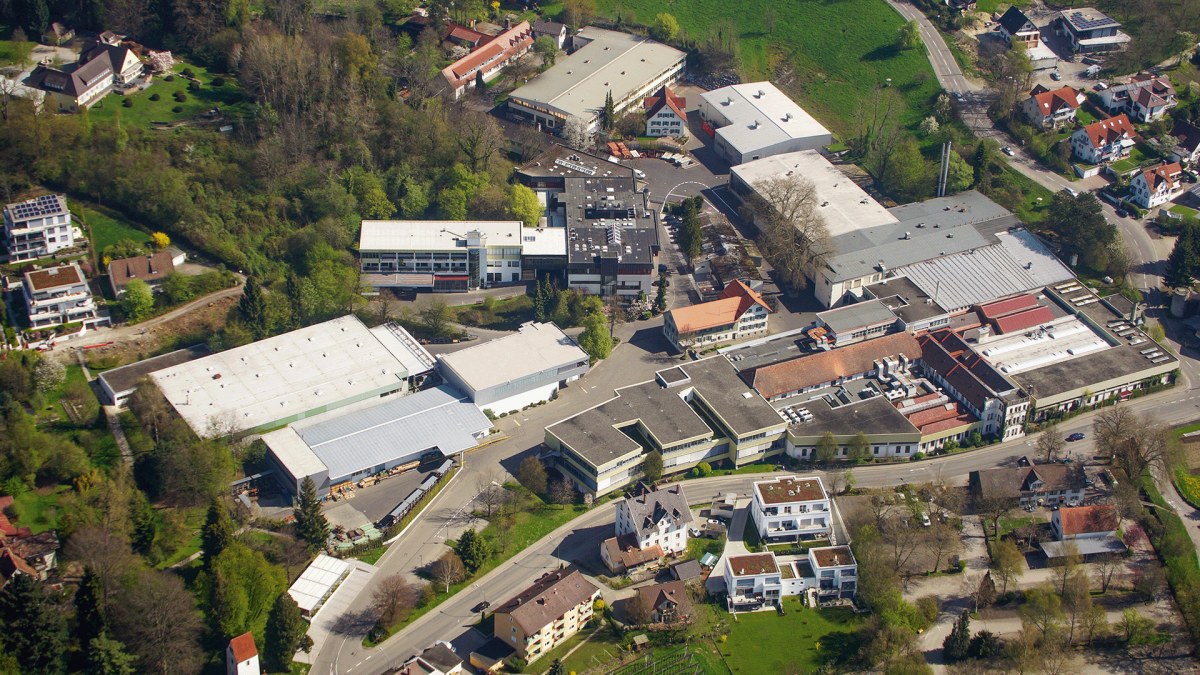
Manual efforts due to central material dispensing
Indirect materials like hand gloves, masks, ear protection, drills, washers and other tools are often issued centrally and manually in companies, which is a lengthy and tedious process. This makes it difficult to ensure transparency about the items being issued and creates a time limit for accessing the required items.
Apart from the classic fasteners and small parts, various tools along with personal protective equipment are also used in the manufacturing of machines and systems of DORNIER. The portfolio comprises over 350 different items ranging from cutters, screwdrivers and safety goggles to gloves, ear protection and masks. Until two years ago, these product groups were issued via a central issuing point at DORNIER. In this process, the warehouse staff assigned the material to the employees, made a record of the material issued and ensured reordering manually – a process chain that involved multiple manual tasks for the purchase department and warehouse staff while also resulting in long wait times for assembly, unnecessary storage of materials and wastage of time. Additionally, the employees were dependent on the location and opening hours of the materials issue department. This is exactly where the vending machine solutions of Würth Industrie Service at DORNIER came into the picture.
Objective of the production supply
- Supply security through automated re-ordering
- 24-hour availability
- Innovative technologies
- Complete transparency of all processes, withdrawals and orders
- Safe and needs-based storage
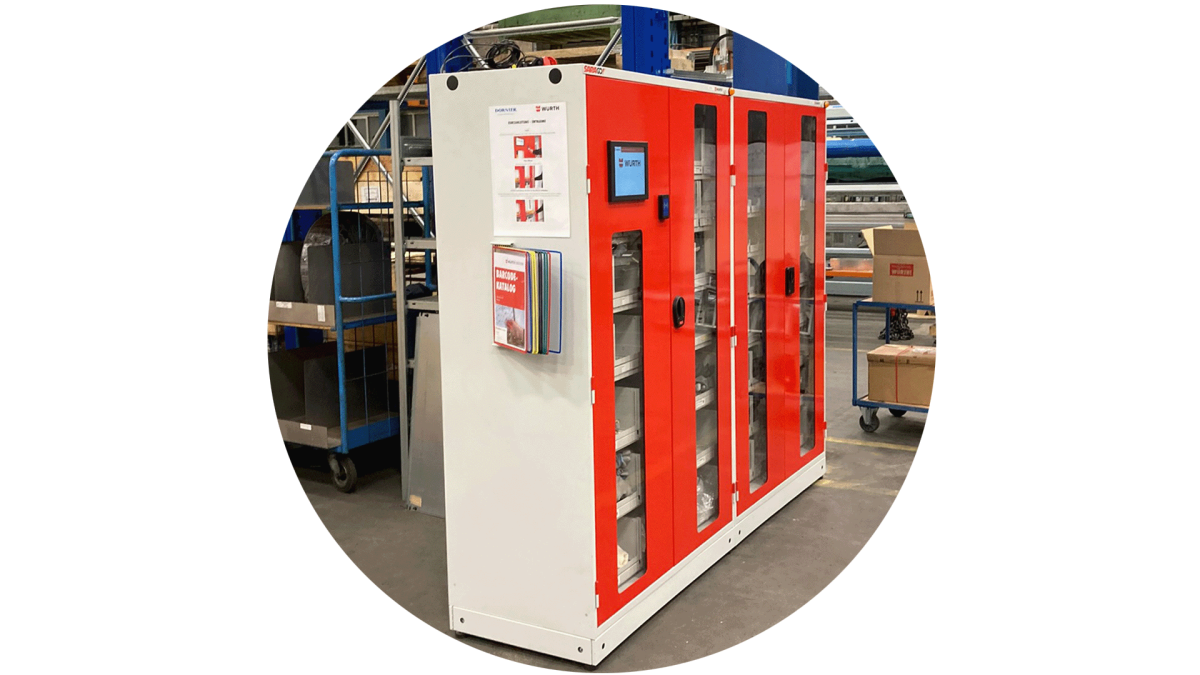
The solution: ORSY®mat
DORNIER discontinued the central issuing point for indirect materials and commissioned ORSY®mat vending machines for over 350 items in its factories in Lindau and Esseratsweiler at a total of eight decentralised withdrawal stations – from the welding shop, sheet metal workshop to final assembly. ORSY®mats are modular and customisable storage vending machines that ensure unlimited supply of materials without space or time restrictions. Installation of the vending machines results not only in increase in item availability, but also in productivity and transparency. The vending machine takes up time-sensitive manual tasks as well as routine tasks for dispensing, replenishment and documentation of consumption that has been previously carried out by the warehouse staff or purchase department. Because of the decentralised positioning in various company divisions, travel times are reduced, which is a significant cost factor.
The vending machines can be integrated perfectly into the material procurement system without the need of any adjustments in the work processes. “The required products are always at hand”, said Melanie Totzauer, Team Lead of Purchase at DORNIER. “Thanks to the high flexibility of the system, we can access tools, occupational safety materials or other consumables. We don’t need to keep track of reordering any more as this is done automatically and in a straightforward manner as well.”. The installed ORSY®mat WGT weighing system (WGT stands for weight) detects the withdrawal of an item with the help of the integrated weighing cells. By using this technology, individual items can be withdrawn without depending on the packaging unit. There is also an option to withdraw multiple items at the same time from the vending machines. After the item is withdrawn, the vending machine closes and takes stock of the complete inside inventory automatically and thus maintains a complete overview at all times. Afterwards, the item data, name and the corresponding withdrawn quantity are automatically transmitted to the Würth system and a logistically optimised restocking process is initiated. Owing to the weighing cells available in different sizes, the system is suitable for managing nearly all types of auxiliary and operating materials. For irregular MRO requirements, Würth Scanners are used in addition to these vending machines.
The result: future-ready and efficient materials management
“Thanks to the high flexibility of the system, we can access tools, occupational safety materials or other consumables. We don’t need to keep track of reordering any more as this is done automatically and in a straightforward manner as well.”- Melanie Totzauer, Team Lead of Purchase at DORNIER
Further success stories of our supply systems
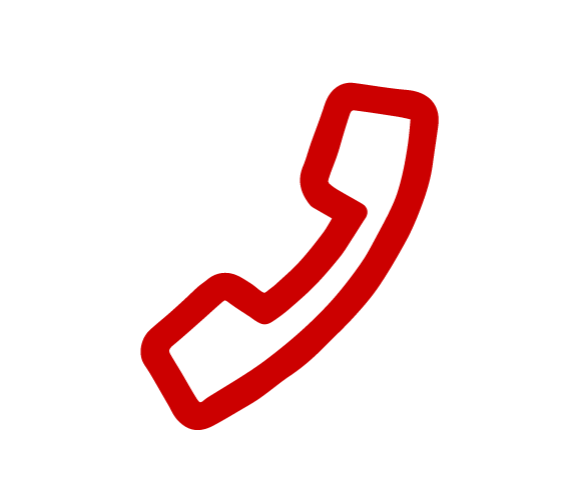
Contact
We are there for you!
Contact us at T +49 7931 91-0 or by e-mail at cps@wuerth-industrie.com.
The Würth Industrie Service GmbH & Co. KG collects and processes the personal data provided in the form in order to process the requested request for you. Please note the mandatory fields in the forms. The legal basis for this processing, the absolutely necessary data, is Art. 6 para. 1 lit. b DSGVO, implementation of a pre-contractual measure. The processing of data voluntarily provided by you is carried out on the basis of Art. 6 para. 1 lit. f DSGVO. Thereafter, processing is permissible which is necessary to safeguard our legitimate interests. Our legitimate interest is to have contact with you, our customers, to improve our consulting quality and to be able to contact you more easily in case of possible queries. The data collected will only be stored by us for as long as is necessary to process your enquiry and to contact you. They are then deleted.
Supplementary data protection information, in particular regarding your rights to information, correction, deletion, restriction of processing, objection and complaint, can be found in our data protection declaration.