Schadensanalyse an Verbindungselementen
Als Spezialist für Verbindungselemente aus Stahl bieten wir Ihnen in diesem Bereich über unser normales Prüfspektrum hinaus auch fallindividuelle Schadensanalysen als nicht akkreditierte Dienstleistung an. Die nötigen Untersuchungen und Prüfungen werden in unserem Labor natürlich soweit möglich akkreditiert abgebildet. Wir sind offen für alle Anfragen und stehen nicht nur für Würth-Produkte zur Verfügung!
Durch eine umfangreiche Schadensanalyse bietet sich für Sie die Möglichkeit, Ursachen von Schäden zu erkennen und spezifische Abstellmaßnahmen zu entwickeln, um ähnliche Probleme in Zukunft zu vermeiden. Eine Schadensaufklärung kann für Ihre Firma einen erheblichen Mehrwert bedeuten!
Schäden können vielfältige Ursachen haben, von Anwendungs- oder Konstruktionsfehlern hin zu werkstoff- oder produktionsbedingten Hintergründen. Durch eine Schadensanalyse können fallabhängig Fehlerursachen und konkrete Abhilfe- und Präventionsmaßnahmen aufgezeigt werden. Als Hersteller finden Sie so Möglichkeiten, die Qualität Ihrer Produkte zu verbessern, wohingegen für geschädigte Anwender und Versicherungen die Suche nach dem Schadensverursacher und somit dem Schuldigen am Schaden interessant ist.
Bei der Schadensanalyse gehen wir fachgerecht nach dem in VDI 3822 festgelegten Ablauf vor. Die Durchführung ist schematisch in Abbildung 1 dargestellt.
In Abstimmung mit Ihnen werden im Rahmen der Schadensanalyse sinnvolle Prüfungen an der Probe mit Hinsicht auf Aufwand und Erkenntnispotential ausgewählt und diese in unserem akkreditierten Labor (oder akkreditierten Partnerlaboren) durchgeführt. Je nach Ergebnislage können weitere Untersuchungen erforderlich sein, um eine aufgestellte Schadenshypothese zu bestätigen oder zu widerlegen. So gehen wir mit unseren Untersuchungen der Schadensursache auf den Grund. Am Ende steht der Schadensbericht, in dem der Schadensfall und die durchgeführten Untersuchungen aufgezeigt werden und je nach Sachlage und Eindeutigkeit der Ergebnisse auch auf Schadensursache(n) und Abhilfemaßnahmen eingegangen wird.
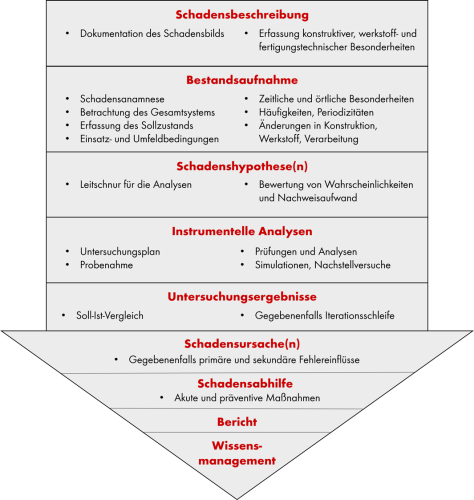
Fallbeispiele
In dieser Rubrik möchten wir Ihnen einige konkrete Beispiele vorstellen, um Ihnen das Vorgehen bei der Schadensanalyse näher zu bringen.
(Hinweis: Die Veröffentlichung der Beispiele wurde mit den betreffenden Kunden abgestimmt. Ohne Einverständnis werden Daten selbstverständlich nicht veröffentlicht.)
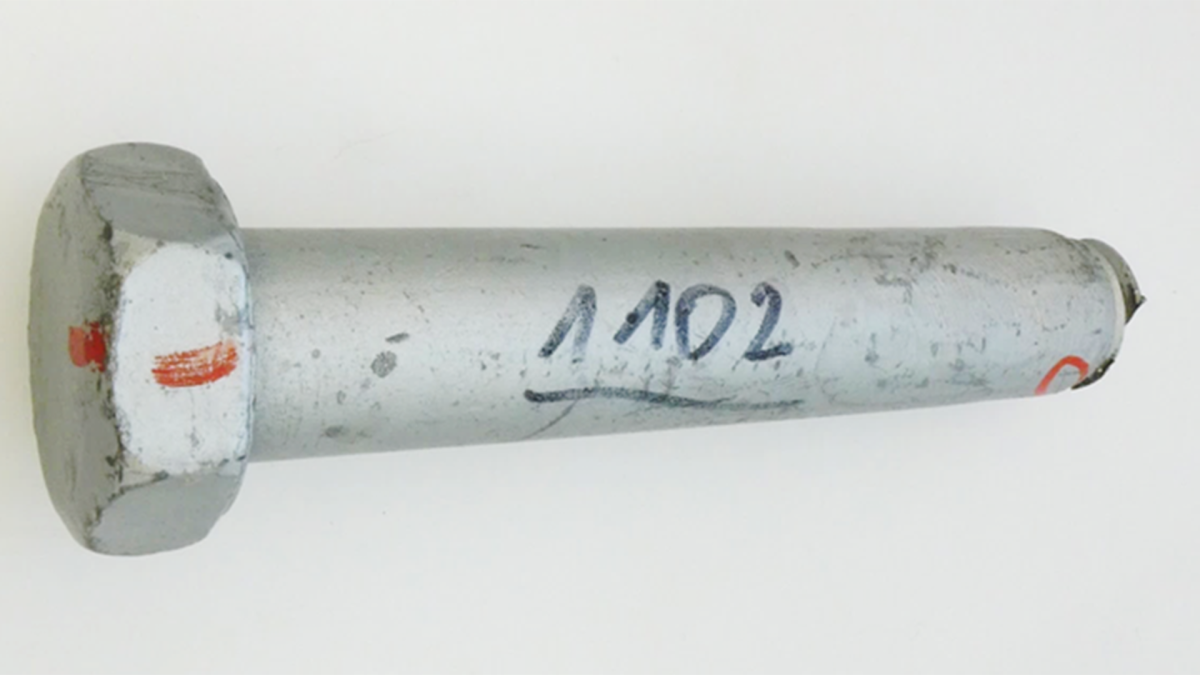
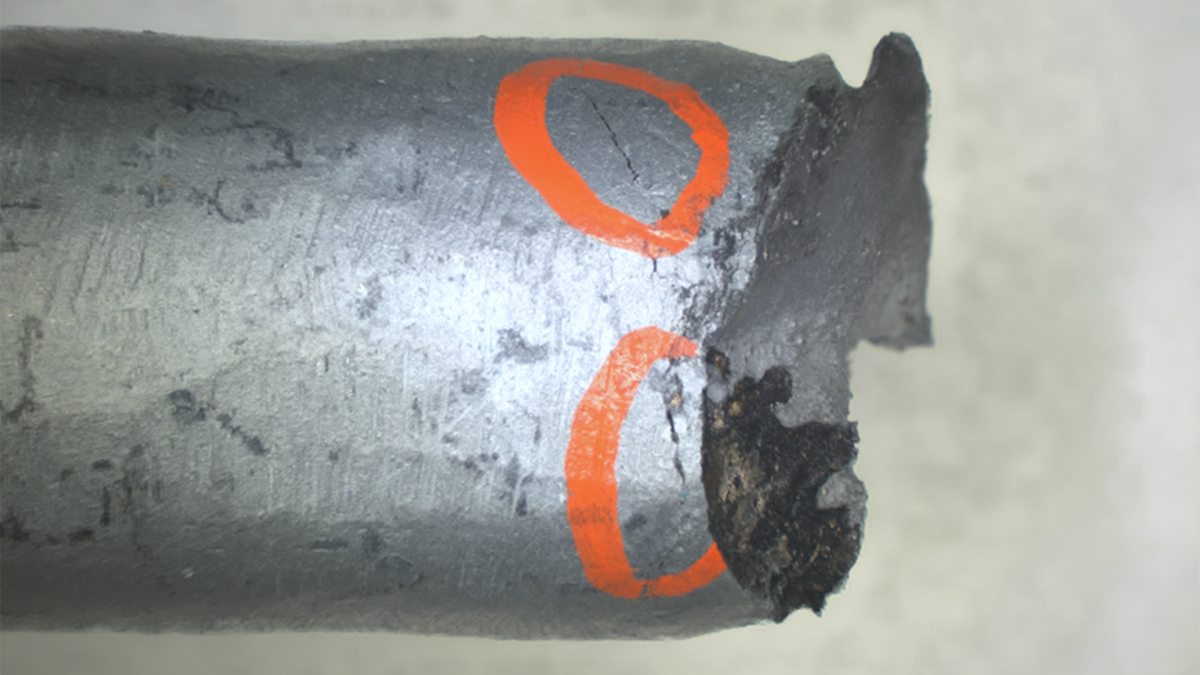
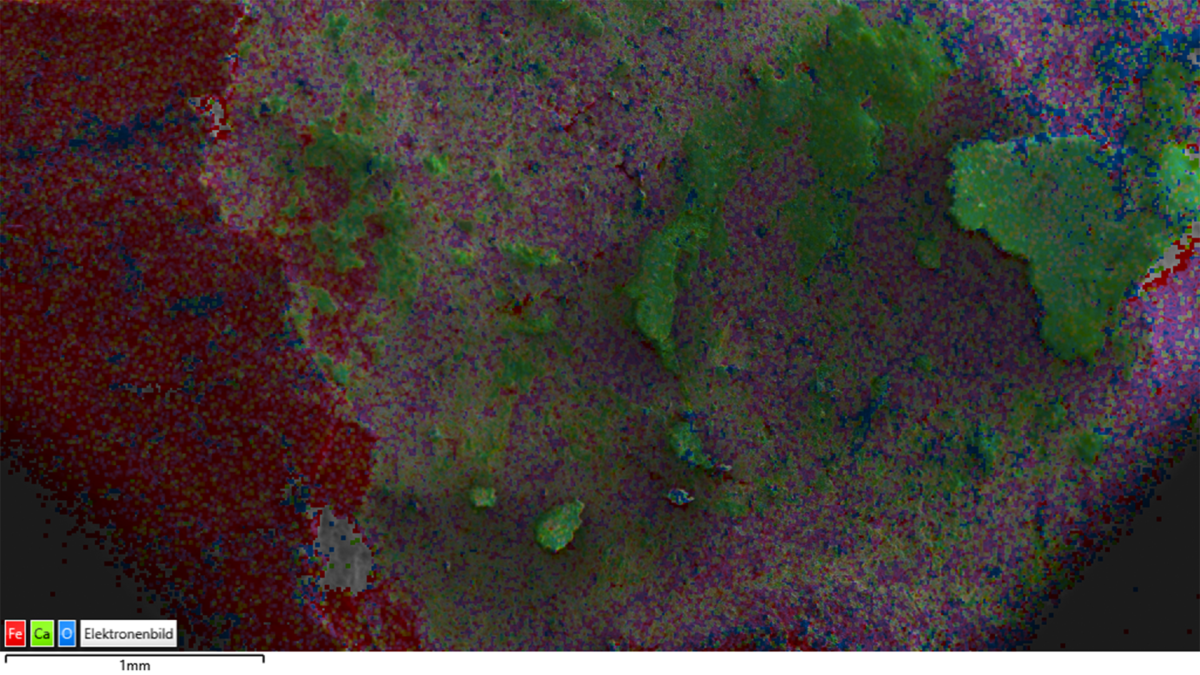
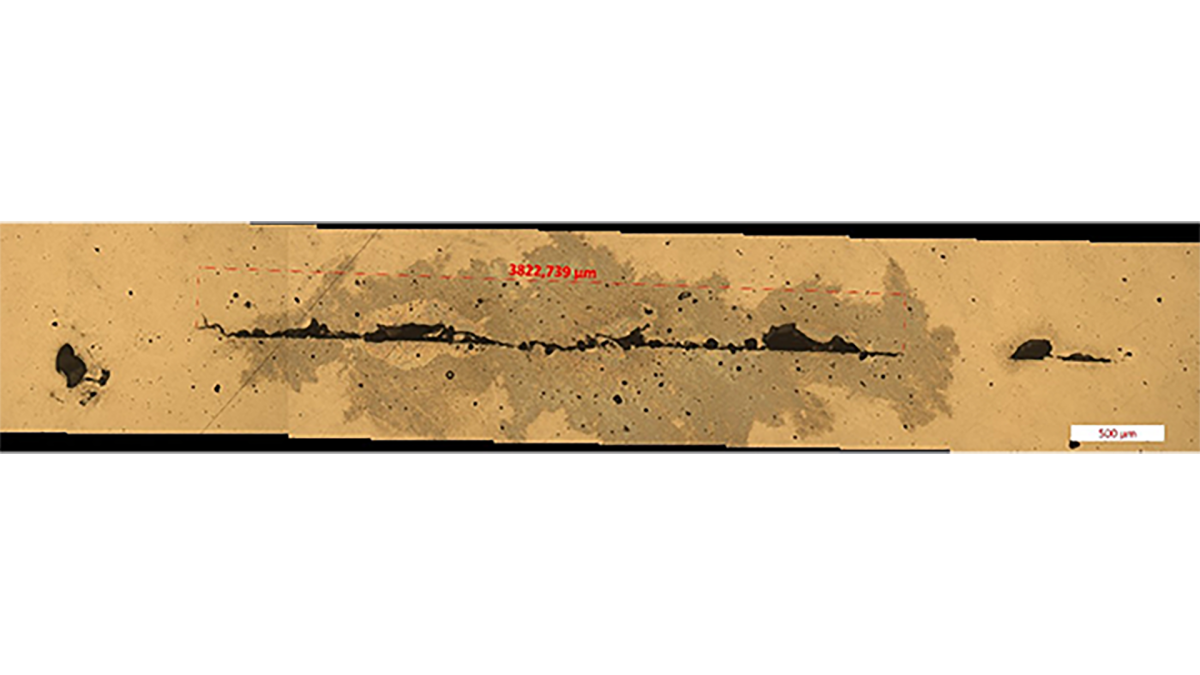
Hintergrund:
Das Labor der Würth Industrie Service wurde mit der Untersuchung einer bei der Montage gerissenen Schraube der Festigkeitsklasse 10.9 beauftragt. Laut Auftraggeber konnten weitere Schrauben der Charge mit dem gleichen Drehmoment erfolgreich montiert werden.
Das Labor hat vom Auftraggeber zusätzlich folgende Informationen erhalten:
- Der Schaft ist oberhalb der Bruchstelle nicht gleichmäßig geformt und weist Bearbeitungsspuren auf
- Optisch sind Nebenrisse erkennbar, die auf dem Muster markiert wurden
Ziel der Untersuchung ist es anhand des zur Verfügung gestellten Musters die Ursache für das Versagen zu bestimmen. Es soll geprüft werden, ob ein Werkstoff- oder Fertigungsfehler vorliegt, der den Schaden verursacht oder begünstigt hat.
Schadenshypothese:
Für den vorliegenden Schadensfall kommen verschiedene Ursachen in Frage: Ein Teil der Bruchfläche ist schwarz verfärbt. Dies tritt typischerweise bei Härtespannungsrissen auf, wenn das Abschrecköl in den geöffneten Riss eindringen kann und dort Rückstände hinterlässt. Härtespannungsrisse treten oft verzweigt auf, wodurch die Nebenrisse entstanden sein könnten.
Es könnte sich allerdings auch um bereits im Halbzeug vorhandene Materialfehler handeln. Hier kommen vor allem Schlackeeinschlüsse in Frage.
In Absprache mit dem Auftraggeber wurden folgende Prüfungen durchgeführt:
- Bruchflächenanalyse
- EDX-Analyse
- Gefügeanalyse
- Geometrieprüfung – Schaftdurchmesser
Im Folgenden sind die Ergebnisse kurz zusammengefasst:
- Torsionsgewaltbruch, schwarzer Bereich ohne Bruchstrukturen
- Schlackerückstände festgestellt, Nachweis über erhöhte Calciumkonzentration im schwarzen Bereich der Bruchfläche
- Nebenrisse enthalten Fremdphasen
- Schaftdurchmesser 19,17 ± 0,02 mm, Differenz zwischen den Messungen sehr hoch, fast alle Messungen kleiner als Toleranzvorgabe
Gekürzte Interpretation / Stellungnahme zu den Prüfergebnissen:
Die Untersuchungsergebnisse legen den Verdacht nahe, dass die gefundenen Materialfehler bereits im verwendeten Vormaterial vorhanden waren. Diese Fehlstellen reduzieren den tragfähigen Spannungsquerschnitt der Schraube und begünstigen die Rissentstehung. Dadurch wurde beim verwendeten Anzugsmoment bereits die effektive Festigkeit der Schraube überschritten.
Meinung:
Die Bearbeitungsspuren sind ein Indiz dafür, dass die Materialfehler während der Fertigung bemerkt wurden und der Versuch unternommen wurde sie zu entfernen.
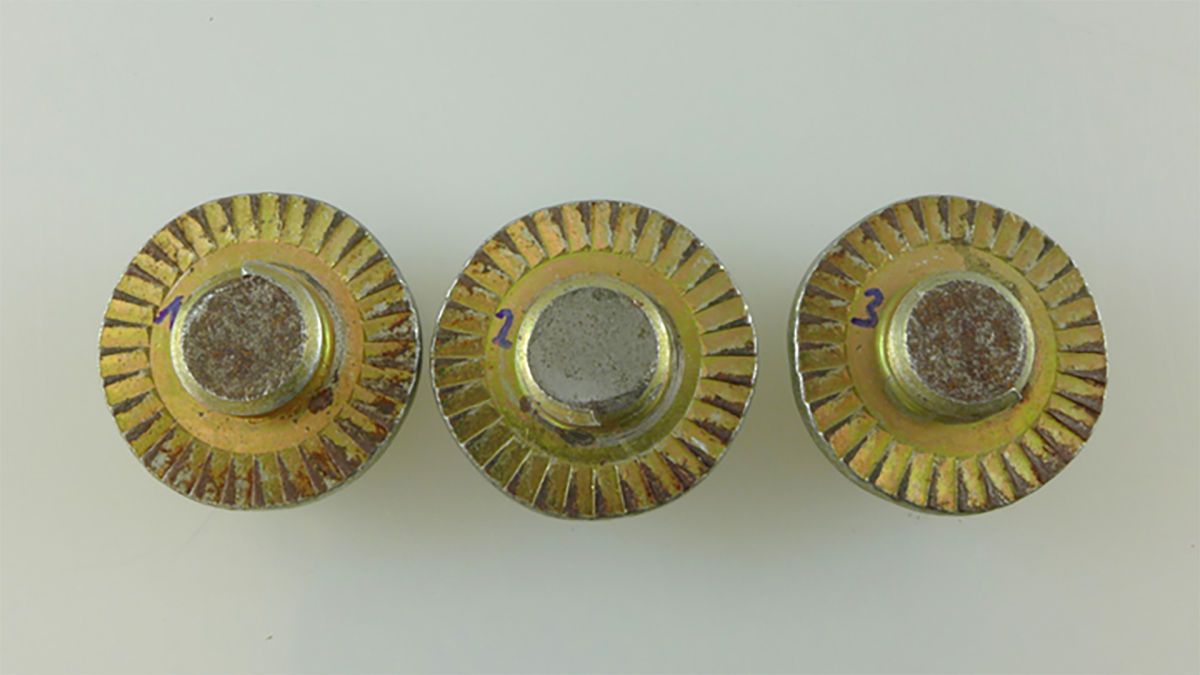
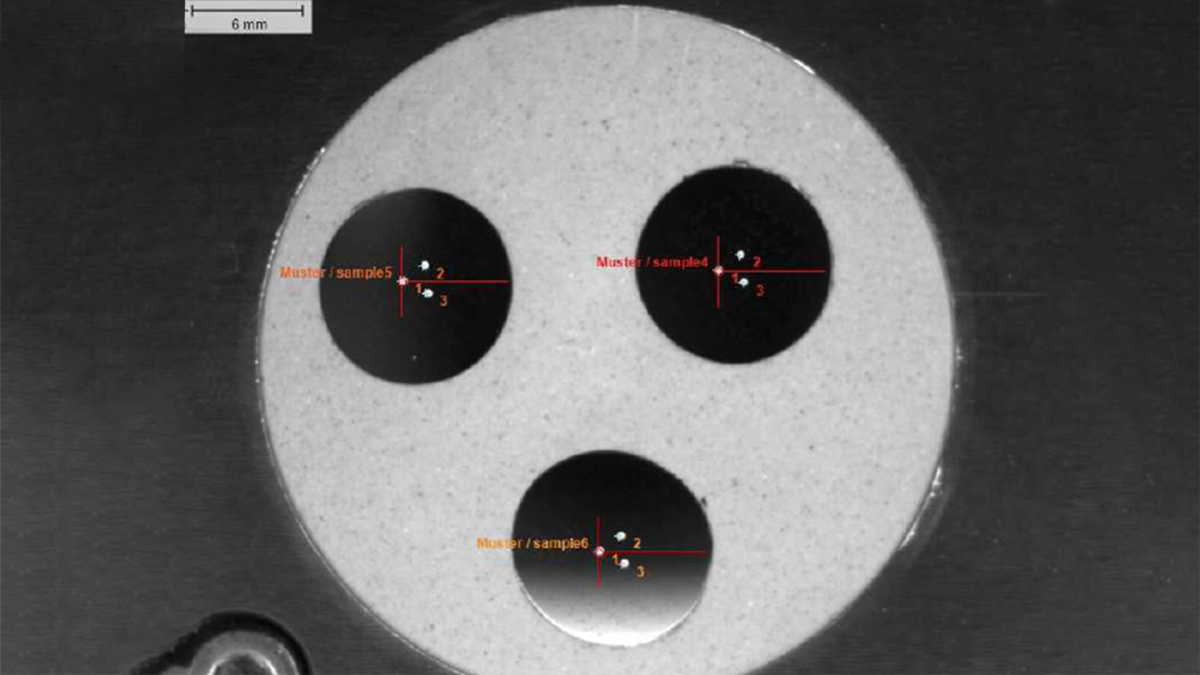
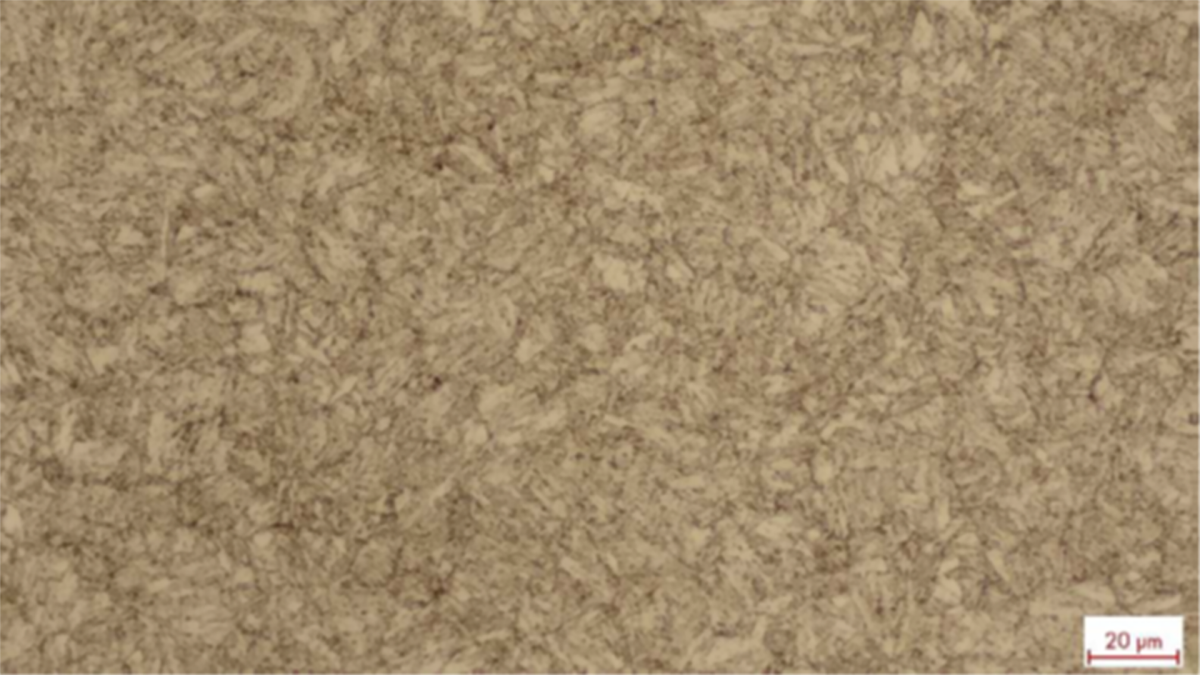
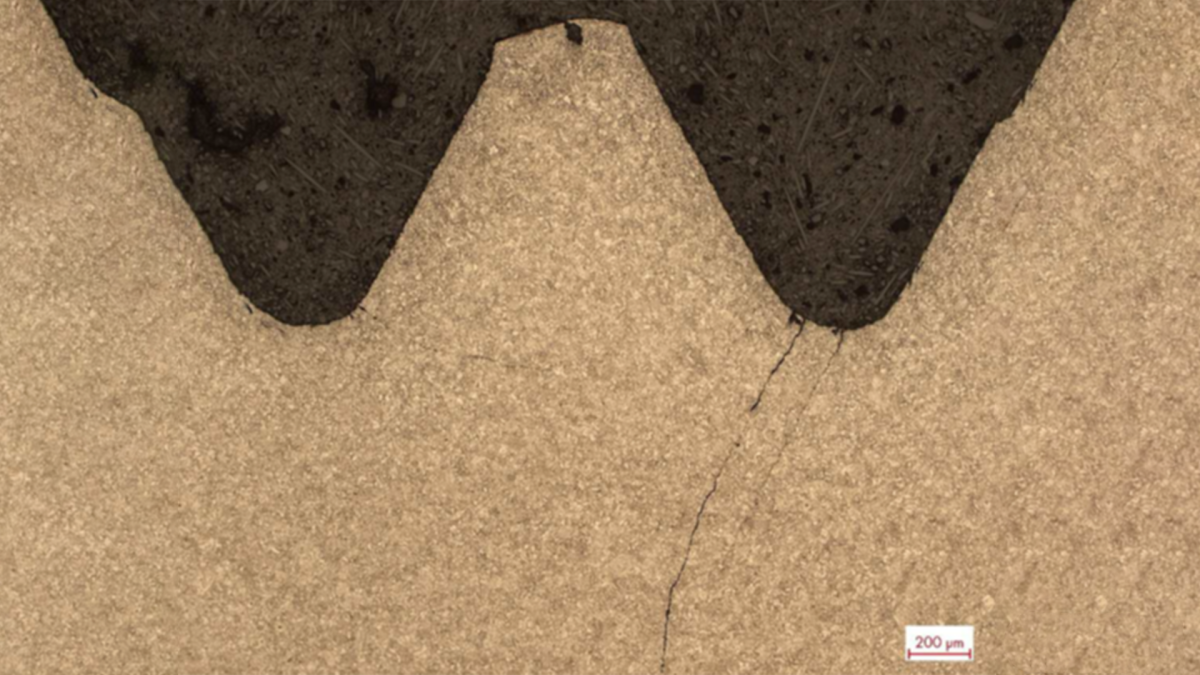
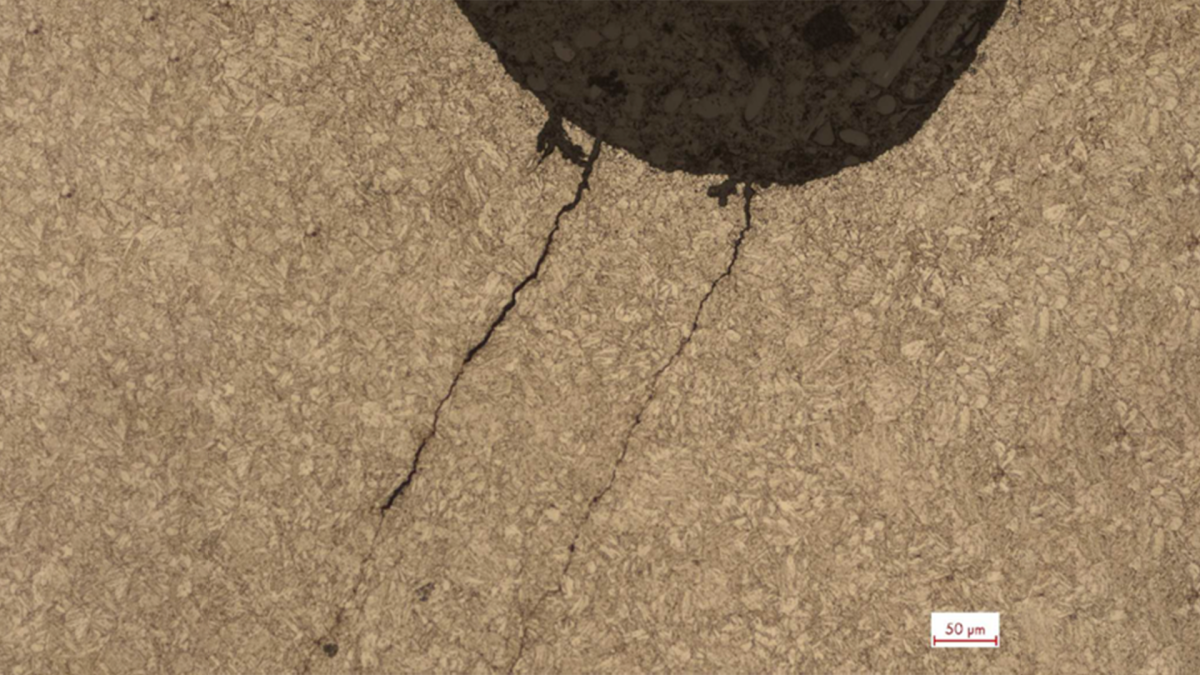
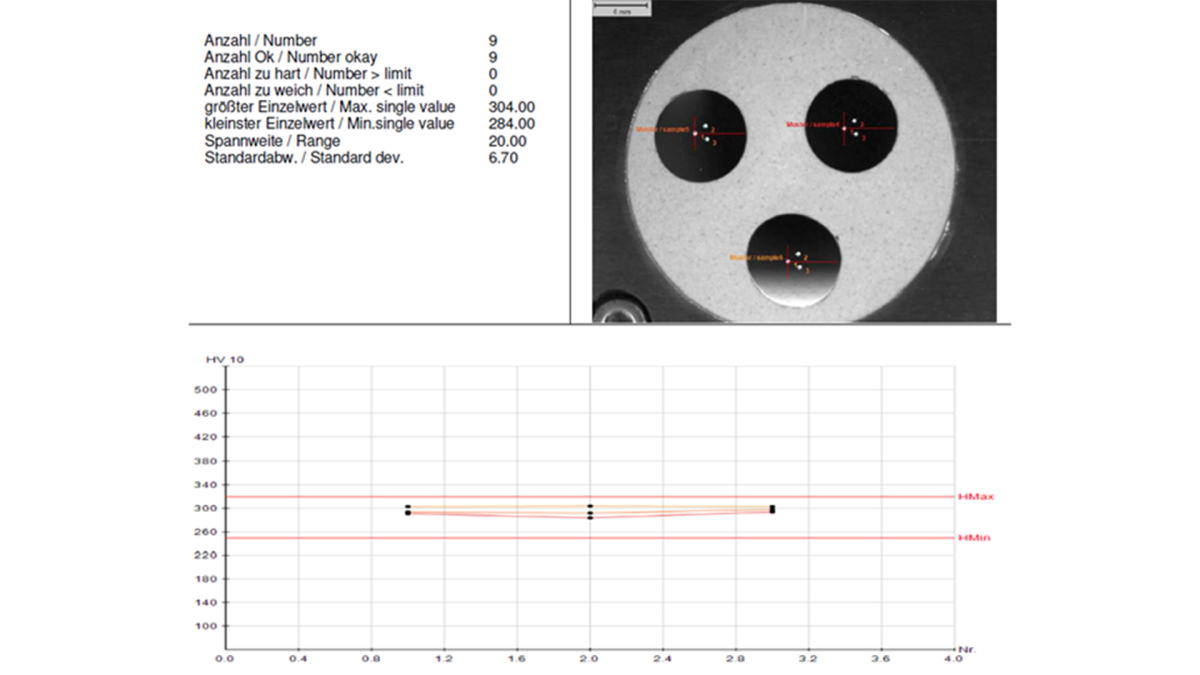
Hintergrund:
Dem Labor der Würth Industrie Service wurden drei Garnituren bestehend aus je einer Schraube und Mutter zur Verfügung gestellt. Die Schrauben wiesen jeweils einen Bruch in Nähe des Kopfes auf. Gegenstand der Untersuchung ist ausschließlich die Schraube.
Ziel der Untersuchung ist es anhand der zur Verfügung gestellten Muster die Ursache für das Versagen zu bestimmen. Es soll geprüft werden, ob ein Werkstoff- oder Fertigungsfehler vorliegt, der den Schaden verursacht oder begünstigt hat.
Schadenshypothese:
Es wird vermutet, dass hier fehlerhafte Materialeigenschaften wie Härte und Gefügestruktur der Grund für den Schaden waren. So könnte z.B. eine zu hohe Härte (v.a. auch im Randbereich) das verformungslose Brechen erklären. Auch die Möglichkeit einer unzulässigen Einsatzhärtung kann nicht ausgeschlossen werden.
In Absprache mit dem Auftraggeber wurden folgende Prüfungen durchgeführt:
- Kernhärteprüfung HV10
- Härteverlauf HV0,3 bzgl. Vorhandensein einer Randschichthärtung
- Gefügeanalyse
- Materialanalyse mittels Funkenspektrometer
Im Folgenden sind die Ergebnisse kurz zusammengefasst:
- Kernhärte Mittelwert 296 HV10
- Randschichthärtung nicht vorhanden, Nachweis über unauffälligen Härteverlauf
- Gefüge aus ca. 90 % Martensit, keine Auf- oder Abkohlung festgestellt, Risse im Gewindegrund festgestellt
- Legierungszusammensetzung entspricht den normativen Vorgaben, keine erhöhten Konzentrationen versprödender Elemente festgestellt
Gekürzte Interpretation / Stellungnahme zu den Prüfergebnissen:
Alle vorliegenden Ergebnisse entsprechen den normativen Vorgaben für Schrauben dieser Festigkeitsklasse. Allerdings wurden bei der Gefügeanalyse tiefe Risse im Gewinde festgestellt, wofür es aber keine normativen Vorgaben bzgl. (Un-)Zulässigkeit gibt. Diese Risse können nicht nur aus der Herstellung der Schrauben, sondern auch z.B. aus Belastungen während der Anwendung resultieren.
Um die Bruchursache zu identifizieren, wurde von uns als weiterführende Untersuchung eine Analyse mit dem Rasterelektronenmikroskop empfohlen. Diese wurde zum damaligen Zeitpunkt von einem externen Partnerlabor übernommen und zeigte auf, dass es sich bei den geprüften Bruchflächen um Schwingbrüche mit relativ geringer Restbruchfläche handelt. Dies deutet darauf hin, dass die Vorspannkraft zum Zeitpunkt des Bruchs gering war. Möglicherweise war die Montagevorspannkraft nicht hoch genug oder die Schrauben haben sich im Betrieb gelockert.
Mittlerweile haben wir auch intern die Möglichkeit, Bruchflächen mit unserem hauseigenen Großkammer-Rasterelektronenmikroskop zu untersuchen und bieten unseren Kunden diese Prüfmöglichkeit gerne an. Sprechen Sie uns einfach an, um zu erfahren, was damit sonst noch alles möglich ist!
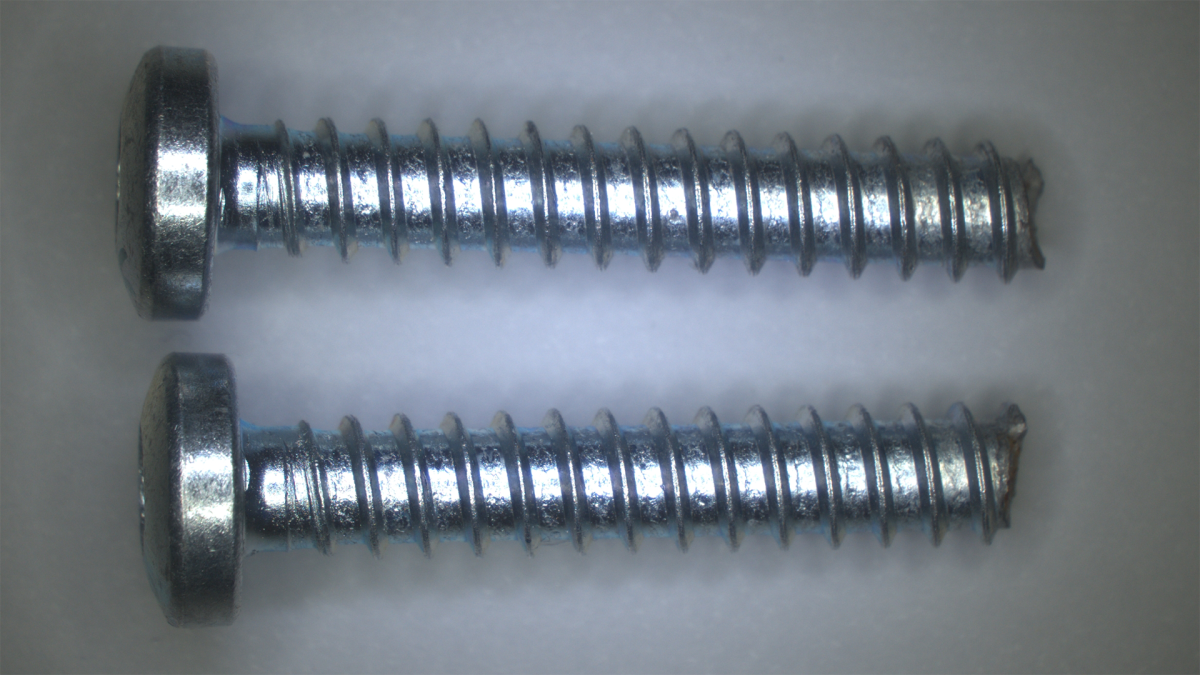
Keine makroskopische Verformung im Bereich des Bruches (rechts im Bild) erkennbar
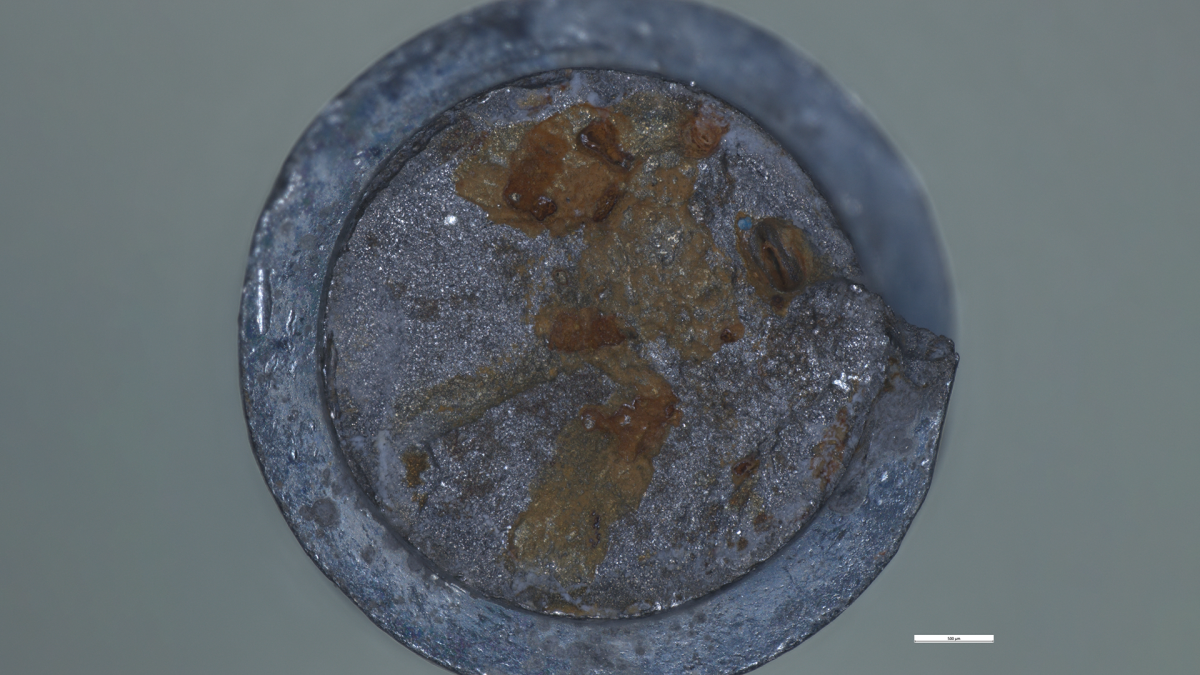
Bruchfläche – Lichtmikroskop
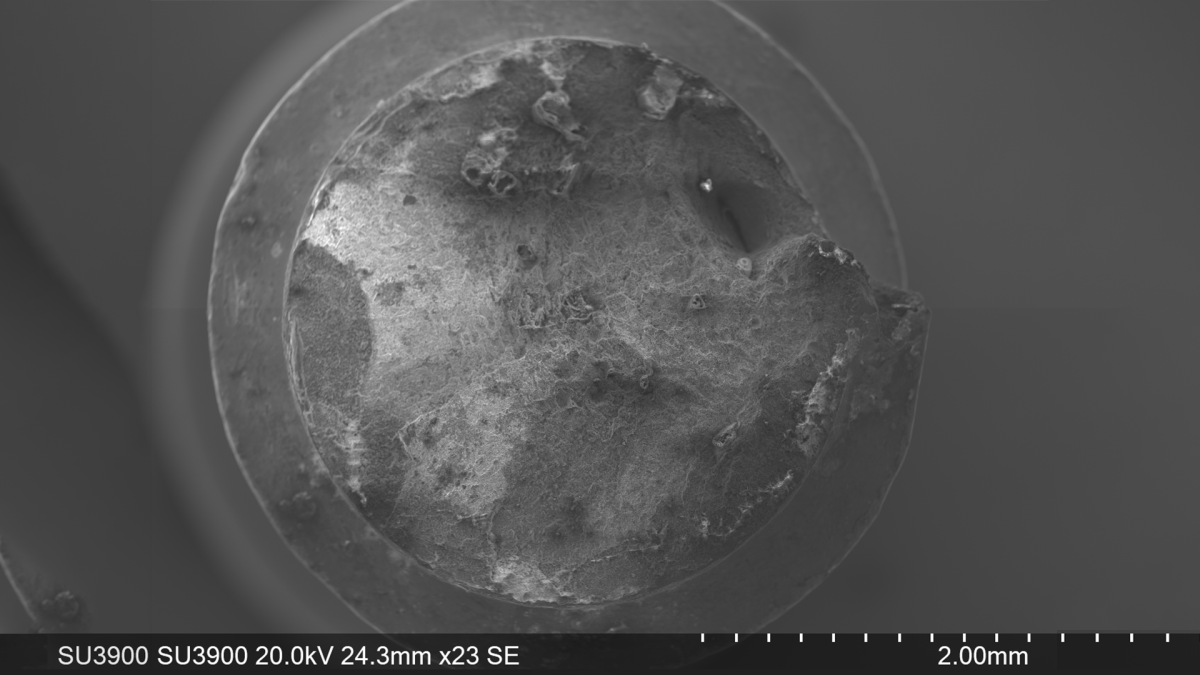
Bruchfläche – REM (Rasterelektronenmikroskop)
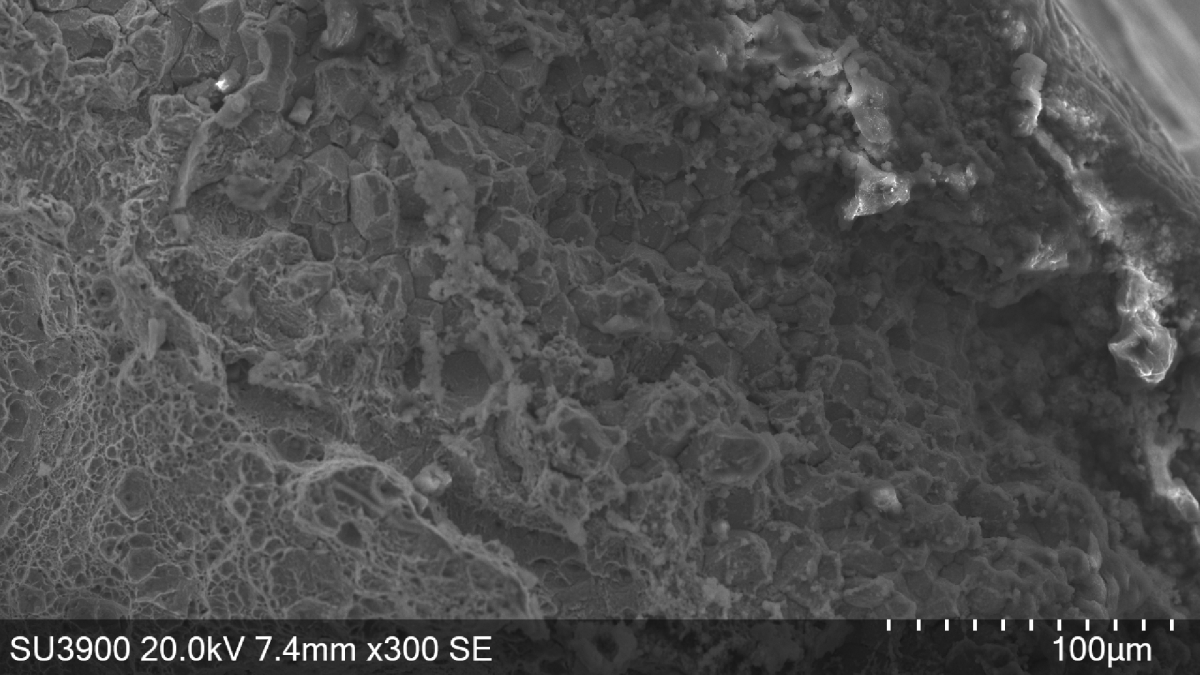
Randbereich Bruchfläche: Übersicht, Übergang vom interkristallin gebrochenen Rand zum in Wabenstruktur gebrochenen Kern, Korrosionsprodukte v.a. in Randnähe
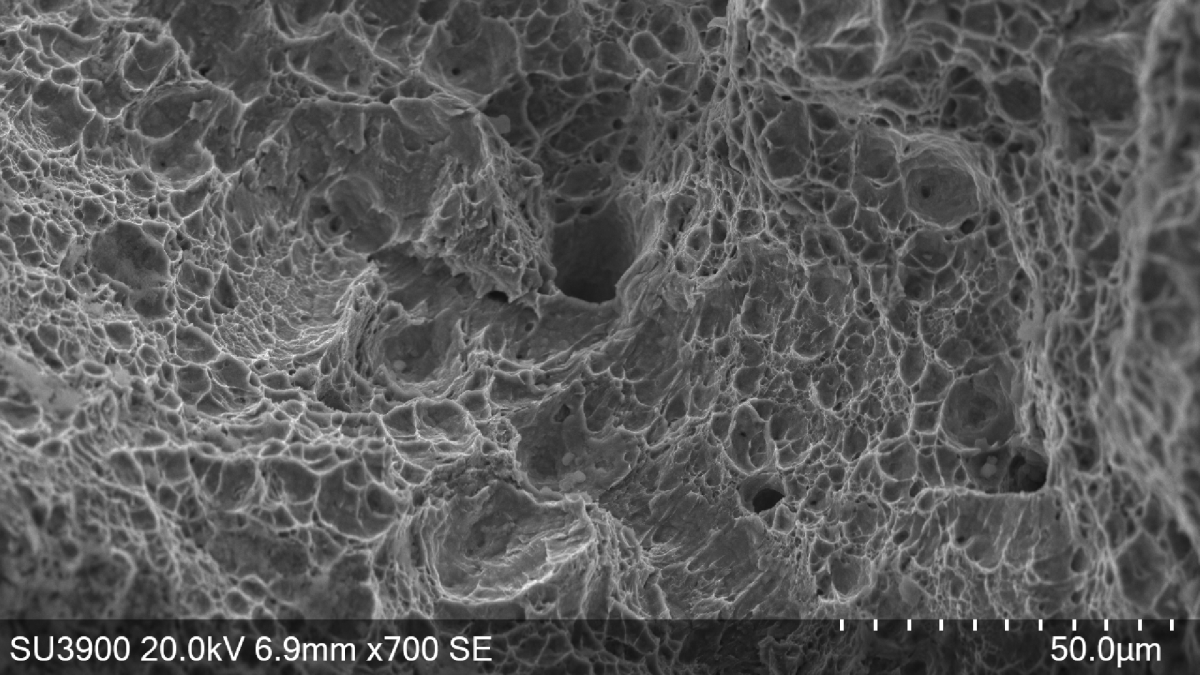
Kernbereich Bruchfläche: Duktile transkristalline Wabenstruktur
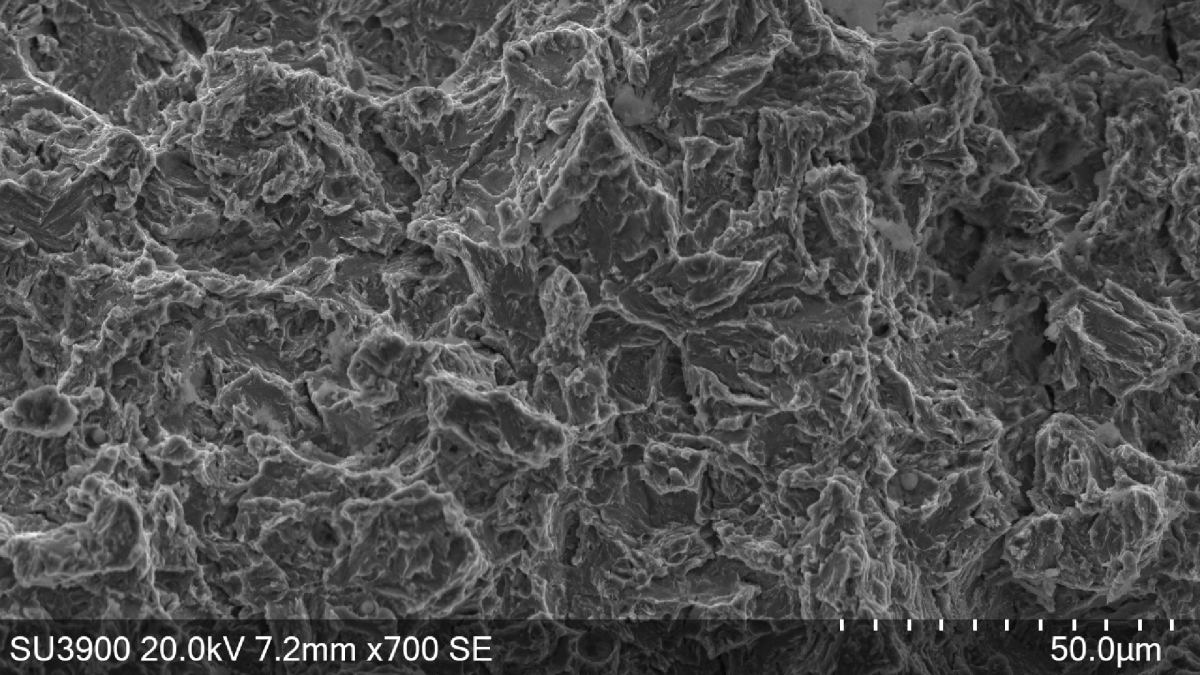
Bereich zwischen Rand und Kern (nur stellenweise in dieser Form ausgeprägt): Spröder transkristalliner Bruch entlang Sekundärkorngrenzen, vereinzelt Korrosionsprodukte
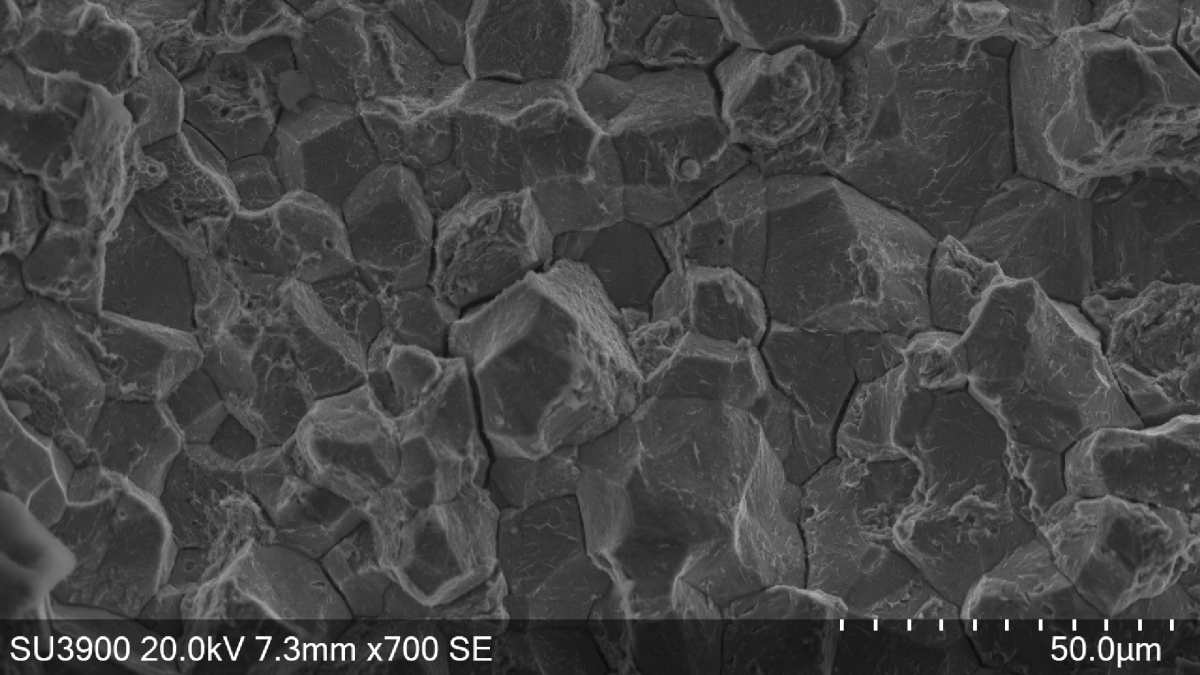
Randbereich Bruchfläche: Spröder interkristalliner Bruch, klaffende Korngrenzen und Restzähigkeiten auf den Kornflächen
Hintergrund:
Das Labor der Würth Industrie Service wurde beauftragt, zwei gebrochene Bohrschrauben (nur Bruchstücke mit Schraubenkopf vorliegend) zu untersuchen. Beide Muster wiesen augenscheinlich Korrosion auf der Bruchfläche auf. Zusätzlich wurde vom Auftraggeber mitgeteilt, dass die Teile nach der Montage gebrochen sind. Es sind auch weitere Schrauben gebrochen, zur Untersuchung wurden allerdings nur zwei Muster zur Verfügung gestellt. Der Kunde beschreibt zudem, dass sich weitere Brüche provozieren ließen, indem Druck auf die verschraubten Teile ausgeübt wurde.
Schadenshypothese:
Die Informationen des Kunden legen nahe, dass die Bohrschrauben etwas zeitverzögert nach der Montage gebrochen sind. Gesicherte, konkrete Daten zum Zeitpunkt des Versagens in Bezug auf den Montagezeitpunkt liegen nicht vor. Unzureichende Informationen stellen leider ein häufiges Problem bei der Schadensanalyse dar, weshalb die Schadenshypothese bestmöglich aufgrund der vorliegenden Angaben aufgestellt werden muss. In diesem Fall lautet die Hypothese, dass der Randbereich der Bohrschrauben versprödet ist und Anrisse entstanden sind. Diese sind aufgrund der nach der Montage anliegenden Vorspannkraft zeitverzögert zu Rissen durch die ganze Schraube angewachsen. Bei den beschriebenen provozierten Brüchen wurde das Risswachstum durch die aufgebrachte Zusatzkraft beschleunigt. Die Versprödung könnte sich aus einer schon vorhandenen Einsatzhärtung der Schrauben oder auch durch den Einfluss von Wasserstoff begründen. Letztgenannte Hypothese wird durch die vorhandenen Korrosionsspuren und auch durch die vorliegende galvanische Beschichtung gestützt, da beides als Wasserstoffquelle dienen kann.
In Absprache mit dem Auftraggeber wurden folgende Prüfungen durchgeführt:
- Bruchflächenanalysen der beiden gebrochenen Musterstücke mittels REM (Rasterelektronenmikroskop)
Im Folgenden sind die Ergebnisse kurz zusammengefasst:
- Ähnliche Bruchmerkmale an beiden Mustern
- Makroskopisch keine Verformung erkennbar, deutet auf spröden Gewaltbruch hin
- Korrosion auf der Bruchfläche, Untersuchung daher nur in nicht korrodierten Bereichen möglich
- Unterschied zwischen Rand und Kern, teilweise auch dem Bereich dazwischen:
- Kernbereich:
Mischbruch aus duktilen Waben und spröden transkristallinen Bruchanteilen bzw. rein duktiler Wabenbruch beim zweiten Muster - Zwischenbereich (nur stellenweise vorhanden): zum Teil duktil in Wabenstruktur, zum Teil spröde mit transkristallinem Bruchverlauf entlang der Sekundärkorngrenzen bzw. als Mischbruch aus diesen Anteilen ausgeprägt
- Randbereich:
spröder interkristalliner Bruch, stellenweise klaffende Korngrenzen und z.T. Restzähigkeiten auf den Kornflächen erkennbar
- Kernbereich:
Gekürzte Interpretation / Stellungnahme zu den Prüfergebnissen:
Die im Randbereich festgestellten klaffenden Korngrenzen und Restzähigkeiten auf den Korngrenzflächen deuten auf einen wasserstoffinduzierten Bruch hin. Dies deckt sich auch mit der aufgestellten Schadenshypothese, die dadurch untermauert wird. Woher der Wasserstoff letztendlich stammte, sei es fertigungsbedingt bei der Beschichtung, bei der augenscheinlichen Korrosion entstanden oder aus anderen Quellen, lässt sich nicht mit Sicherheit sagen. Durch die vermutlich im spröden Randbereich entstandenen Anrisse kommt es zum Bruch der gesamten Schraube. Die duktilen Bereiche im Kern stellen die verbliebenen nicht versprödeten Anteile der Schraube dar, die aber nicht mehr ausreichend tragfähig waren, um unter der anliegenden Last zu bestehen.
Da die o.g. Anzeichen für Wasserstoffversprödung nicht überall erkennbar waren, ist auch ein zusätzlicher Einfluss einer Versprödung durch die angenommene Einsatzhärtung nicht auszuschließen. Das Bruchbild ist hier erfahrungsgemäß ähnlich, allerdings ohne o.g. Anzeichen. Um diese Theorie näher zu untersuchen, könnte zusätzlich eine Gefügeanalyse durchgeführt werden, um die Einsatzhärtung nachzuweisen. Dies wurde in diesem Fall allerdings nicht beauftragt.
Auch geometrische Probleme, wie z.B. ein scharfkantig ausgeführter oder überwalzter Gewindegrund könnten schadensbegünstigende Faktoren darstellen. Die Muster wurden allerdings nicht daraufhin untersucht.
Was Sie noch interessieren könnte:
Die Würth Industrie Serivce GmbH & Co. KG erhebt und verarbeitet die in dem Formular angegebenen personenbezogenen Daten, um für Sie die gewünschte Anfrage zu bearbeiten. Bitte beachten Sie bei den Formularen die Markierung der Pflichtfelder. Rechtsgrundlage für diese Verarbeitung, der zwingend erforderlichen Daten, ist Art. 6 Abs. 1 lit. b DSGVO, Durchführung einer vorvertraglichen Maßnahme. Die Verarbeitung der von Ihnen freiwillig mitgeteilten Daten erfolgt auf der Grundlage von Art. 6 Abs. 1 lit. f DSGVO. Danach ist eine Verarbeitung zulässig, die zur Wahrung der unserer berechtigten Interessen erforderlich ist. Unser berechtigtes Interesse besteht darin, mit Ihnen, unseren Kunden, Kontakt zu haben, unsere Beratungsqualität zu verbessern und Sie bei möglichen Rückfragen einfacher kontaktieren zu können. Die erhobenen Daten werden von uns nur solange gespeichert, wie es für die Bearbeitung Ihrer Anfrage sowie zur Kontaktaufnahme mit Ihnen erforderlich ist. Danach werden sie gelöscht.
Ergänzende Datenschutzhinweise, insbesondere zu Ihren Rechten auf Auskunft, Berichtigung, Löschung, Einschränkung der Verarbeitung, Widerspruch und Beschwerde, finden Sie in unserer Datenschutzerklärung.